Research
Ammonia synthesis project | Crystalline materials synthesis project
Ammonia synthesis project
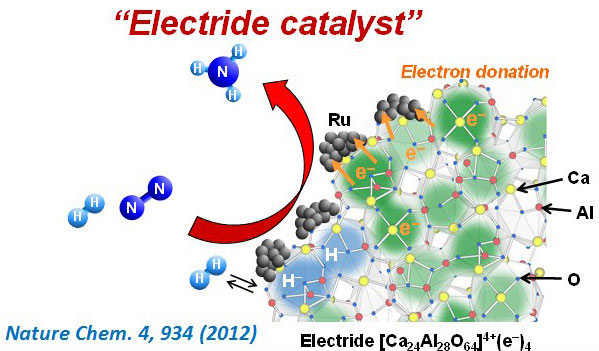
Mass production of ammonia was first made possible by the establishment of the Haber-Bosch process some 100 years ago. Today, worldwide ammonia production exceeds 170 million tons annually and continues to grow. The invention of this process served to ensure a plentiful supply of chemical fertilizers (nitrogen-based fertilizers) essential for food production and today is responsible for supporting a global population of over 7 billion. Moreover, ammonia has become a focus of attention in recent years because it can be liquefied at room temperature under 10 atmospheric pressure, which allows for its use as an easily stored and easily transported energy carrier. This has made the goal of reducing energy consumption in ammonia production even more important than it was before. In research motivated by this context, we have created catalysts based on a new material, 12CaO·7Al2O3 electride (C12A7:e-), which offers a new route for ammonia production with a low environmental burden. Our proposed catalyst material, Ru/C12A7:e–, which consists of Ru nanoparticles fixed in C12A7:e–, facilitates the efficient dissociation of N2 molecules—due to powerful electron injection—and functions as a catalyst for ammonia production at rates that exceed those of traditional catalysts by an order of magnitude, and with half the activation energy. Moreover, because hydrogen poisoning—the greatest disadvantage of Ru catalysts—may be suppressed in these catalysts, their efficiency in ammonia synthesis does not decrease under pressurized conditions. After this result was published in Nature Chemistry, it was reported in publications including Chemical Sciences News in RSC Advances—as well as Japan’s Yomiuri Shimbun and Nikkei Shimbun newspapers—and was recognized as a “Notable Accomplishment” by Japan’s Cabinet Office.
Crystalline Materials Synthesis Project
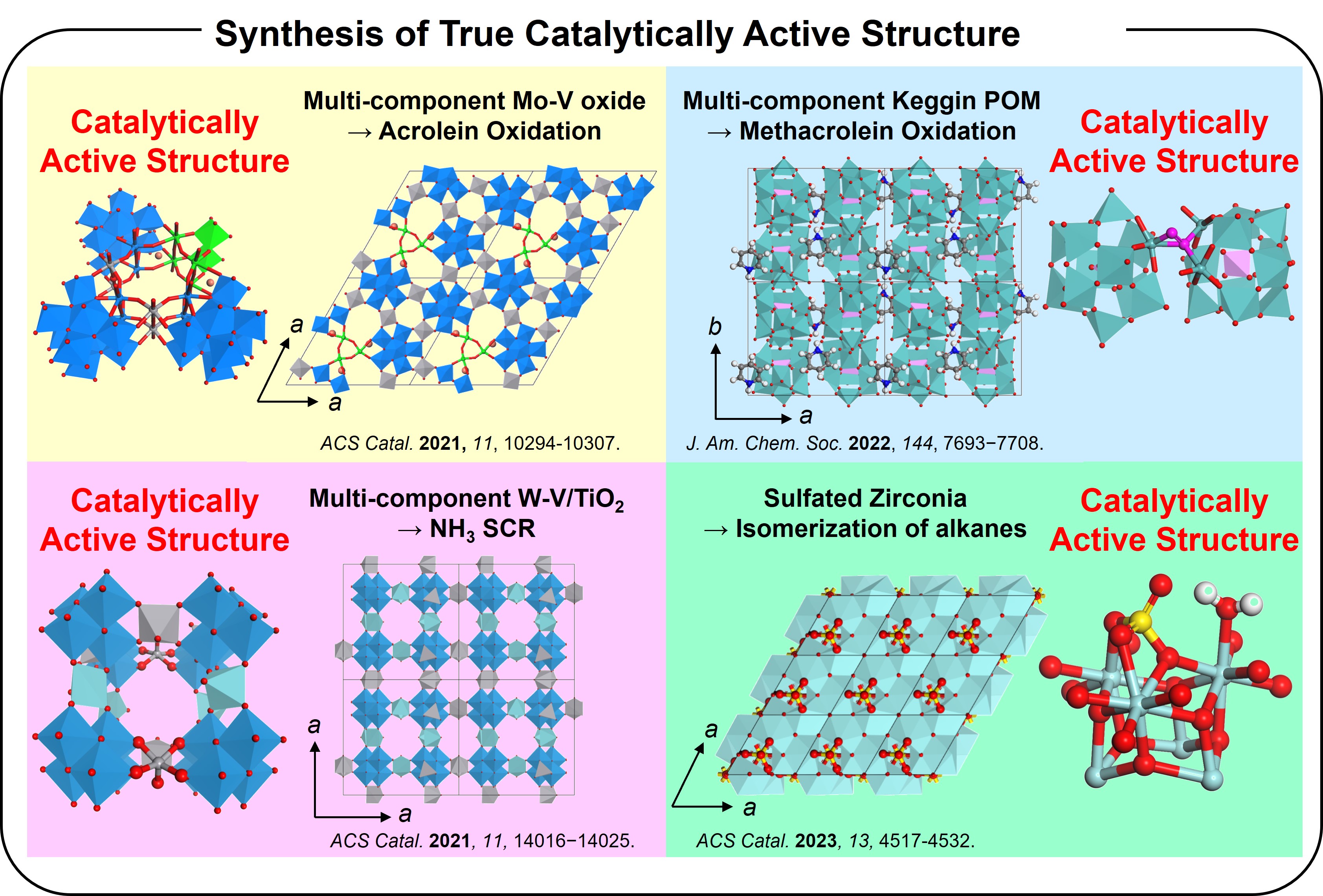
Solid catalysts are used in many chemical industrial processes and are truly essential materials. However, much remains unclear about "where and how" the catalytic functions are generated. The reason for this lies in the history of solid catalyst development. In the early 1900s, during the development of catalytic chemistry, the main focus was on the mass production of useful chemicals. As a result, performance was the primary requirement for catalysts, and many metal elements were used to enhance performance. Consequently, numerous solid catalysts with excellent performance were developed, greatly enriching people's lives. However, the catalysts developed during this period were composed of multiple elements, resulting in highly complex structures. This complexity made it extremely difficult to clarify where and how catalytic functions were generated. To address this, we focused on the material synthesis. We hypothesized that if we could develop crystalline solids with simple structures that still exhibit excellent catalytic performance, the homogeneous nature of the solid-state catalysts would allow us to investigate "where and how" the catalytic reactions occur within the structure. Based on this concept, we successfully developed crystalline catalysts that exhibit excellent catalytic activity even compared to industrial catalysts in various reactions, such as alkane selective oxidation, selective oxidation of unsaturated aldehydes, NOx reduction using NH3, and alkane isomerization. By utilizing these catalysts, we demonstrated that catalytic reactions proceed within beautifully organized local structures. This research provides a fundamental understanding for catalytic chemistry and paves a way for rational design of industrial catalysts. We continue to work diligently every day to uncover the true nature of solid catalysts.